Low-speed Unmanned Driving based on Solid-state LiDAR
Author: Release time:2022-01-13 09:45:04
According to incomplete statistics from some Chinese Driverless Industry Research Institute, in 2021, the autonomous driving industry around the globe will disclose more than 200 important financing events, with total financing of nearly 150 billion yuan (including IPO). Among them, low-speed driverless product and solution suppliers have raised nearly 70 financings, exceeding 30 billion yuan. The rapid development of low-speed unmanned driving is inseparable from the support of LiDAR technology. So, does solid-state LiDAR really have the ability to move towards mass application in the scenarios of low-speed unmanned driving?

There are many types of LiDARs. The current classification methods commonly used in the industry are mainly defined based on whether there are mechanical rotating parts inside the LiDAR. They are roughly divided into three types: mechanical, solid-state, and hybrid solid-state. The traditional mechanical LiDAR has been used for a long time and the technology is more mature. It is the mainstream of the current industry application, but due to the structural characteristics, it is difficult to break through in terms of service life and cost. In the autonomous driving laboratory stage, due to the small demand, the application does not have high requirements for the service life and cost of the LiDAR. The mechanical LiDAR can basically meet the needs of this stage. However, from the laboratory to the batch application, factors such as service life, cost, and even appearance have been taken into consideration by the companies.
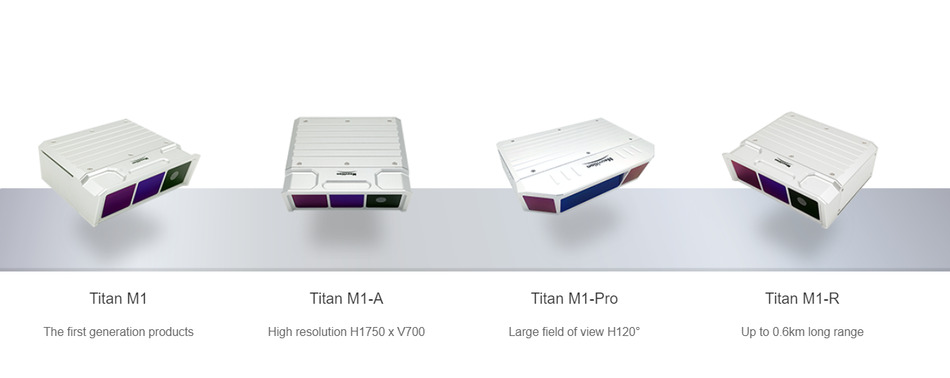
As traditional mechanical LiDARs gradually fail to meet the needs of the large-scale application in autonomous driving, solid-state LiDAR routes that are different from traditional mechanical rotation methods have begun to attract attention. Compared with mechanical LiDAR, without the mechanical structure of complex high-frequency rotation, the durability of solid-state LiDAR has been greatly improved, and the size can be greatly reduced. From the perspective of product design, solid-state LiDAR basically avoids the problems of current mechanical LiDAR, but solid-state LiDAR also has shortcomings, such as small field of view, immature technology, upstream parts supply problems, and so on.
Question 1: Whether the solid-state LiDAR performance can meet the needs and replace the mechanical LiDAR
Solid-state LiDAR is more optimized than mechanical LiDAR in terms of performance such as detection distance, resolution, and accuracy. At present, compared with mechanical LiDAR, the advantage of solid-state LiDAR is mainly that the solid-state structure design makes the LiDAR more stable and helps to save the assembly space in the system so that the LiDAR size can become small. Due to its smaller size, solid-state LiDAR can be better integrated into low-speed unmanned drivings.
The main performance indicators of LiDAR can be divided into detection distance, detection accuracy, field of view, and service life.
In terms of detection distance, generally, the current solid-state LiDAR can achieve the longest distance of about 200m, and even some LiDARs such as the Neuvition Titan M1-R solid-state LiDAR has a detection distance of 600m. However, most of the requirements for detection distance in low-speed unmanned driving scenarios are not high, generally, 10-50 meters can be satisfied so that the detection distance of solid-state LiDAR can fully meet the needs of low-speed unmanned driving scenarios.
In terms of detection accuracy, most mature solid-state LiDARs can reach centimeter-level, which is similar to mechanical LiDARs. In fact, in some scenarios of low-speed unmanned driving, such as mining areas and unmanned delivery, the requirements for accuracy are not high, and solid-state LiDAR can also meet the needs of these scenarios.
In terms of field of view (FOV), most semi-solid-state and solid-state LiDARs can only achieve a horizontal field of view scanning of 120°at the highest, while mechanical ones can achieve 360°scanning.
In terms of service life, since most of the existing solid-state LiDARs are aimed at the automotive-grade market, a lot of adaptive designs have been made for product stability and reliability. For example, the service life of Neuvition solid-state LiDAR products is 50,000 hours, far longer than that of mechanical LiDAR.
On the whole, the most important aspect of limiting the application performance of solid-state LiDAR is field of view (FOV). Mechanical LiDAR mainly drives the overall rotation of the optomechanical structure through the motor, which can achieve 360° scanning, but semi-solid-state and solid-state LiDAR can scan the horizontal field of view up to 120°.
How to ensure the vehicle can achieve 360° perception and detection with solid-state LiDAR solution? The solid-state LiDAR manufacturers might use “splicing” solution. Through the splicing of several solid-state LiDARs, 360°scanning, high-precision mapping, and precise positioning can be achieved in low-speed unmanned driving scenarios such as handling AGVs. In fact, the splicing solution will have advantages over mechanical ones in some application scenarios. For outdoor heavy haul AGVs with flat-panel handling vehicle bodies, the LiDAR can only be installed under the vehicle, there will also be scanning blind spots for mechanical LiDARs, so the splicing of multiple mechanical LiDARs is also required. In this case, the splicing solution of small-size solid-state LiDAR will be more flexible, and the cost will be less.
In August 2021, the first 5G+ Beidou navigation outdoor unmanned AGV launched by Tianjin Langyu is also equipped with two solid-state LiDARs, which are mainly used for perception and obstacle avoidance. “Because the operation scene of outdoor AGV is relatively empty, the requirements for detection distance will be higher. The detection distance of ordinary solid-state LiDAR can fully meet the needs of outdoor AGV low-speed unmanned driving.”
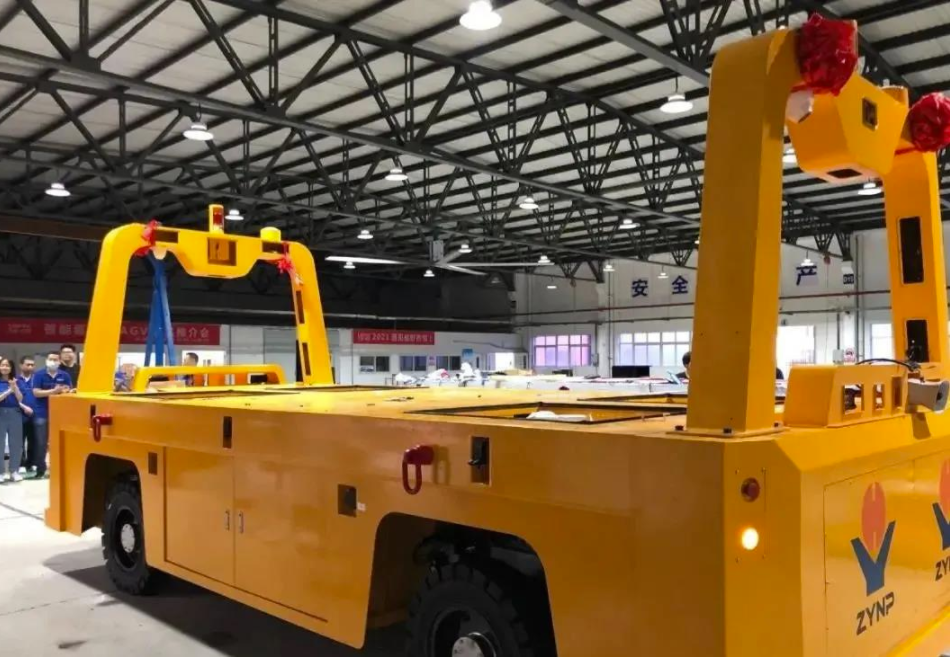
Question 2: Is solid-state LiDAR cost really a competitive advantage?
In most of the current low-speed unmanned driving sensor configuration solutions, the cost of LiDAR accounts for more than 60%, and some even reach 70%-80%. From the perspective of cost, LiDAR has a great impact on the price of a complete unmanned vehicle. Therefore, the price of LiDAR is also the key factor affecting the current enterprises’ selection for LiDAR. The splicing solution mentioned above solves the field of view problem of solid-state LiDAR, but what follows is the question of the cost-effectiveness of solid-state solutions. In the splicing solution, at least 3 solid-state LiDARs are needed to achieve the effect of a mechanical LiDAR. From the perspective of product unit price, the price of solid-state LiDAR is undoubtedly lower than that of mechanical ones, but the price of mechanical LiDARs is also declining, is the cost of multiple solid-state LiDARs really competitive compared to a single mechanical LiDAR?
Neuvition Technology‘s answer is “yes”. At the beginning of technical route selection and product design, one of the core concepts pursued by Neuvition is cost control. Our current series of solid-state LiDAR products have more advantages in cost than mechanical LiDAR. In the future, with our further mass production capabilities, there will be room for the price reduction. The cost must be a very important influencing factor in the process of mass application, whether it is used for a low-speed unmanned driving car or a passenger car. With the maturity and close cooperation of the entire industry chain, solid-state LiDAR prices will continue to decline.
On the basis that the performance can meet the demand and the cost has advantages, with the mass application of low-speed unmanned driving, can solid-state LiDAR be mass-produced to meet the increasing market demand? In fact, some Chinese and US solid-state LiDAR manufacturers have already achieved mass production and are continuously improving their mass production capabilities. Neuvition is currently laying out a vehicle-grade solid-state LiDAR production line, with a designed production capacity of about 30,000 units/year. With the expansion of the scale and the improvement of the manufacturing process, the leading LiDAR manufacturers will lead a group of supply chain companies to jointly stand out and provide LiDAR products with superior performance, reliability, and durability. The improvement of performance and quality will bring about further expansion of scale and reduction in cost.
In addition, while developing products with higher performance and lower cost, the ability of LiDAR manufacturers to respond to the needs of car companies, continue to provide services and iteration will be the core competitiveness in the era of mass production.